W warunkach dynamicznie rozwijających się procesów nowoczesnej gospodarki, tworzenia coraz bardziej złożonych branż i procedur kontrolnych, jednym z najbardziej odpowiednich podejść do ich poprawy jest wprowadzenie metod optymalizacji różnych strat. Przede wszystkim dotyczy to zasobów przedsiębiorstw - tymczasowych, finansowych, technologicznych, energetycznych i innych.
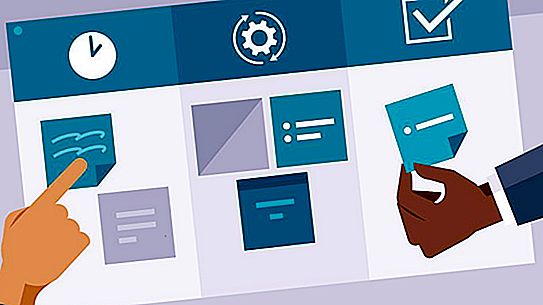
Funkcje działania
W praktyce istnieje pewien pułap związany z poziomem rozwoju technologicznego i organizacyjnego systemu (organizacja, przedsiębiorstwo). Oczywiste jest, że niepraktyczne jest wymaganie całkowitej automatyzacji produkcji z małego warsztatu do szycia ubrań według różnych kryteriów, a zwłaszcza ekonomicznych. Jednak niezależnie od wielkości systemu konieczne jest zapewnienie maksymalnego i optymalnego wykorzystania dostępnych zasobów przy minimalnych stratach, co jest prawdą w przypadku wszystkich organizacji i działań.
W takim przypadku konieczne jest zastosowanie technik progresywnej kontroli procesu, które są oparte na teorii tworzenia ubogiej lub szczupłej produkcji. Należą do nich systemy 5S i TPM, mapowanie strumienia wartości i SMED itp.
Cel innowacji
Lean („lean”) produkcja to system specjalnych podejść do organizowania działań, który uważa za swój główny cel eliminację strat o innym charakterze w systemie. Mechanizm jest dość prosty: wszystko, co nie stanowi wartości dodanej dla klienta, powinno zostać zaklasyfikowane jako niepotrzebne (strata) i wyeliminowane z systemu. Oczywiste jest, że kamieniem węgielnym jest koncepcja „straty”, ponieważ ich definicja będzie miała bezpośredni wpływ na skuteczność metody. W tym przypadku szkolenie w zakresie mapowania przepływu tworzenia wartości dla ich specjalistów jest znaczącą zaletą na rynku świadczenia usług
Rodzaje strat
Lean Manufacturing jest jedną z podstawowych koncepcji logistyki produkcji. I chociaż istnieje kilka różnych podejść do określania strat, wyróżniamy najbardziej uniwersalne typy:
- Czas oczekiwania - wszelkie przerwy w działaniu zmniejszają wartość produktu końcowego. Oczekiwanie na naprawy materiałów, sprzętu, informacji lub wskazówek od kierownictwa spowalnia proces i zwiększa koszty jego wdrożenia.
- Niepotrzebne operacje (niepotrzebne przetwarzanie produktów) - niepotrzebne operacje technologiczne, etapy projektów, wszystko przewidziane w standardowych procedurach, ale można je wyrównać bez utraty zaufania klientów.
- Niepotrzebny przepływ pracowników - poszukiwanie narzędzi, sprzętu, irracjonalne ruchy z powodu złej organizacji miejsca pracy itp.
- Niepotrzebny przepływ materiałów - zła organizacja systemu magazynowego, brak postępowej logistyki transportu i mechanizmów outsourcingu zaopatrzenia materiałowego i technicznego.
- Nadwyżki zapasów - wiązanie kapitału obrotowego organizacji w wyniku wysokich kosztów nadwyżek pozycji w magazynie.
- Straty technologiczne - przestarzałe systemy przetwarzania danych, procesy technologiczne i trasy przetwarzania.
- Straty z nadprodukcji - wytwarzanie nadmiernych ilości produktów, co prowadzi do wzrostu kosztów magazynowania, transportu i późniejszej sprzedaży.
- Straty intelektualne - brak mechanizmów zachęcających do inicjatywy pracowników i pracowników, słaby system propozycji racjonalizacji, tłumienie twórczego podejścia do pracy.
Jedną z najczęstszych metod eliminacji strat w systemie i optymalizacji procesów realizacji projektu jest mapowanie strumienia wartości. Lean Manufacturing pozwala stworzyć system adaptacyjny, który elastycznie reaguje na zmiany w otoczeniu.
Strumień wartości
Strumień wartości jest zbiorem wszystkich działań (operacji) wykonywanych na produkcie w celu osiągnięcia pożądanego stanu lub uzyskania wymaganych właściwości. Działania są podzielone na dwie grupy:
- tworzenie wartości produktu (wartość dodana);
- nie tworzy wartości produktu.
Jak widać na przedstawionym rysunku, etapy zmiany technologicznej produktu (kolor niebieski) zwiększają wartość produktu, a etapy operacji pomocniczych - przygotowania, transportu, przechowywania - (kolor różowy) - wręcz przeciwnie, raczej zmniejszają wartość produktu z powodu niepotrzebnej straty czasu.
Proces mapowania
Podstawą techniki mapowania jest opracowanie specjalnego algorytmu graficznego, który pokazuje proces tworzenia produktów (realizacji projektu) w czasie. Algorytm ten nazywany jest mapą strumienia wartości, która jest modelem graficznym opartym na określonym zestawie znaków (znaków, symboli).
Główne zalety karty:
- uzyskanie graficznego modelu trwającego procesu, z uwzględnieniem różnych dodatkowych procesów dla całościowej percepcji wizualnej (zadaniem jest zobaczenie ogólnego przebiegu zdarzeń);
- zdolność do wykrywania różnego rodzaju strat na wszystkich etapach projektu;
- możliwość parametrycznej optymalizacji wynikowego modelu w celu zminimalizowania wszelkiego rodzaju kosztów;
- pracować z różnymi wskaźnikami algorytmu, które znajdą wyraz w poprawie rzeczywistych procesów.
Tworzenie odwzorowania strumienia wartości na podstawie standardowych wykresów i symboli - prostokątne i trójkątne bloki, strzałki kierunkowe i krokowe oraz inne kształty. Umożliwia rejestrowanie etapów badanego procesu w języku wspólnym dla wszystkich specjalistów. Jednocześnie zaleca się różnicowanie symboli w zależności od danego przepływu - materialnego lub informacyjnego.
Mechanizmy mapowania strumienia tworzenia wartości w lean manufacturing pozwalają nam zidentyfikować wszystkie miejsca gromadzenia niepotrzebnych elementów.
Zasady budowania
Mapowanie przepływu tworzenia wartości wiąże się z wdrożeniem szeregu prostych kroków, które pozwolą ci szybko stworzyć pożądany model projektu o określonych parametrach. Na przykład:
- Analiza przepływów materiałów i informacji w celu uzyskania wiarygodnego obrazu bieżącego stanu procesu.
- Przepływaj w kierunku do przodu i do tyłu, aby zidentyfikować ukryte przyczyny strat i znaleźć negatywne wzorce.
- W żadnym wypadku nie dokonuj pomiarów czasu samodzielnie, nie polegając na wynikach innych specjalistów lub standardowych wartościach.
- Jeśli to możliwe, utwórz mapę również na własną rękę, co pozwoli uniknąć błędów innych i rozwiązań szablonowych.
- Skoncentruj się na samym produkcie, a nie na działaniach operatorów lub sprzętu.
- Zbuduj mapę ręcznie za pomocą ołówka lub markerów.
- Wizualizuj elementy procesu za pomocą kolorów, aby poprawić postrzeganie.
Przykłady mapowania strumienia wartości
Rozważ przykład tworzenia mapy przepływu w dziedzinie przepływu pracy nieodłącznie związanej z działalnością dowolnej instytucji.
Głównym zadaniem jest wybór najlepszego dostawcy. Standardowy proces decyzyjny jest następujący: wybór dostawcy (12 dni) - wykonanie tekstu umowy (3 dni) - zatwierdzenie przez służby funkcjonalne (18 dni) - wiza osoby upoważnionej (3 dni) - uzyskanie pieczęci głowy (1 dzień) - uzyskanie podpisu kontrahenta (7 dni) - rejestracja w urzędzie (3 dni).
Łącznie otrzymujemy niezbędny czas na uzyskanie wymaganej umowy - 48 dni. Rezultatem analizy było odkrycie wąskich gardeł w schemacie decyzyjnym.
Główne zmiany po analizie mapy:
- Wydano polecenie przekazania podpisu części dokumentów szefom działów (zmniejszenie obciążenia aparatury kontrolnej i znaczne zmniejszenie liczby zatwierdzeń).
- Te same wymagania zostały opracowane dla wszystkich usług (wspólne zrozumienie wymagań dotyczących dokumentów kontraktowych, zmniejszając liczbę błędów wykonawców).
- Wdrożono przekrojową zasadę analizy dokumentacji, tworząc wspólną grupę specjalistów z różnych usług.
- Zastosowano nowe szablony umów.
- Zoptymalizowane mechanizmy dokumentacji poprzez system elektroniczny.
- Opracowano elektroniczny system śledzenia jakości dokumentów przechodzących przez etapy procesu.
Głównym rezultatem mapowania przepływu tworzenia wartości było dwukrotne skrócenie czasu potrzebnego na uzyskanie dokumentacji kontraktowej, w tym czasu koordynacji w służbach departamentalnych.